UNIT-1 INTRODUCTION ( COST ACCOUNTING)
SYNOPSIS:
- ELEMENTS OF COST ( THEORY & PROBLEMS IN COST SHEET)
- MATERIAL PURCHASE PROCEDURE
- STORAGE OF MATERIALS ( INCLUDING PROBLEMS)
- METHODS OF INVENTORY CONTROL
- METHODS OF PRICING OF ISSUES ( INCLUDING PROBLEMS)
- LABOUR- CLASSIFICATION & ACCOUNTING FOR LABOUR COST
- METHODS OF REMUNERATION ( INCLUDING PROBLEMS)
- OVERHEADS-MEANING, CLASSIFICATION, ALLOCATION, APPORTIONMENT AND ABSORPTION ( INCLUDING PROBLEMS)
Introduction:
Cost: Cost is the amount incurred for the production and distribution of the product. It does not include income tax, interest on capital, preliminary expenses, dividends, goodwill, bad debts etc.
Cost Accounting: Recording of cost-related information.
Costing: Costing is the method or technique with the help of which cost can be ascertained.
Definition:
Cost accounting is defined as a system of recording in accounts the materials used and labour employed in the manufacture of a certain commodity/ on a particular job.
Objectives:
- Ascertainment of cost
- Determining selling price
- Control of inefficiencies
- facilitates the preparation of financial statements
- provides the basis for operating policies
1Q) Elements of cost: The various elements of cost can be illustrated by the following chart.
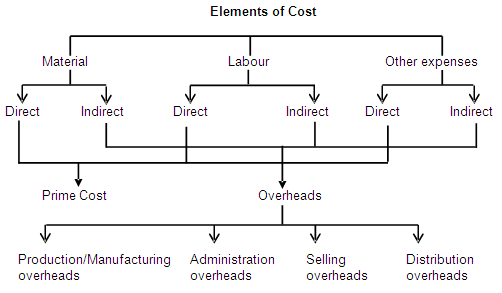
Material: The substance from which the product is made is called material. It can be direct as well as indirect.
Direct material: Direct materials are those materials which can be identified in the product and can be conveniently measured and directly charged to the product. Thus, these materials directly enter production and form a part of the finished products.
Examples: Clay in bricks, timber in furniture making, and bricks in building a house.
Indirect material: Indirect materials are those materials which cannot be traced as part of the product. Indirect materials include fuel, and oil required for operating and maintaining plant and machinery.
Example: nuts and bolts, tools etc.
Labour: In order to convert materials into finished products, human effort, is required, such an effort is known as labour. Labour can be direct, as well as indirect·
(i) Direct labour: Labour which is directly involved in the production of goods & services and which can be conveniently allocated to a Job, process/commodity unit.
Example: wages paid to driver, conductor etc, of a bus in transport office.
(ii) indirect labour: Indirect labour is labour which is not directly engaged in the production of goods & services but which indirectly helps the direct labour engaged in production.
Example: Mechanics, supervisors, cleaners
(iii) Other Expenses: These may be classified as direct and indirect
(i) Direct Expenses: These are expenses which can be directly, conveniently & wholly identified with a Job, process / productive expenses.
Example: Hire of special machinery required for a particular expense.
(ii) Indirect expenses: These Expenses cannot be directly, conveniently & wholly allocated to cost centres.
Example: Rent, lighting, Insurance charges etc.
Overheads: Any expenditure over& above prime cost is known as overhead. In general terms, overheads comprise all expenditure incurred for/in connection with the general org. of the whole/ part of the undertaking that is the cost of operating supplies & services used by the undertaking including the maintenance of capital assets.
Overhead may be defined as " The cost of indirect material, indirect Labour & such other expenses including services as cannot conveniently be charged to a specific unit. The major business functions are as follows:
1. Production overhead
2. administration overheads
3. selling overheads
4. distribution overheads
1. Production overheads: These costs are also known as manufacturing overhead, factory overheads/works overheads. They are the aggregate of the indirect expenses of operating the production
division of concern and include all indirect expenses incurred
to convert the raw material into the finished product.
Examples: factory power, cotton waste, consumable stores, depreciation and insurance of plant and machinery and factory building and maintenance, indirect wages etc
(ii) Administration overheads: The other term used is general/ office overheads. These include all such Expenses connected with the direction, control and administration functions of the business excluding those connected with the selling distribution functions.
Examples: office rent and rates, office lighting & heating, office salaries, audit fees, postage & telephone, printing and stationery, legal charges, depreciation of office building & machinery etc.
(iii) Selling overheads: This type of expenditure is incurred in promoting sales & retaining customers. It is that portion of the marketing cost, is incurred in serving orders.
Example: Advertisement, salesmen salaries, brokerage and commission, bad debts, showroom expenses, travelling expenses:
(iv) Distribution overheads: The expenditure incurred from the time Product is completed in the factory until it reaches The market or customer is classified as distribution overheads.
Examples: Packing & shipping expenses, carriage outwards, warehousing costs, delivery van costs etc.
2Q) Material Purchase Procedure:
Almost in any industry, a huge portion of working capital is invested in the business in the form of inventories. of the different types of inventories, materials occupy the key position in respect of the amount of investment involved in them. The important role played by this element of cost in the total cost structure of a product only through analysis of the total cost of production
Materials, for instance, account for as much as 56 to 69% of the total cost of production, so, it is very necessary to buy the raw material at a low cost. If we reduce 10% the cost of buying raw materials, it means eve have increased our 10% profit. purchase department will make full planning of its purchase. Everything should be planned what to buy, when to buy and how to buy. By using the material purchase procedure, we can reduce our costs.
Organizational structure for purchasing: In a small concern, all the functions including purchasing are generally performed by the owner himself. But in a large manufacturing firm, an efficient purchasing department should be entrusted with buying. The head of the department is known as the purchase manager.
Organizational structure for purchasing: 1. Centralised purchasing 2. De-Centralized purchasing
1. Centralised purchasing: It refers to the purchase of materials by a single purchase department. This department is headed and managed by a purchasing manager. Under centralized purchasing, all purchases are made by the purchasing department to avoid duplication, overlapping and non-uniform procurement. A company has to follow the centralized purchasing of materials ensuring proper materials control as well as efficient storekeeping. Under this system, the purchasing department purchases the required materials for all the departments and branches of the company.
Advantages of centralized purchasing:
- A bulk quantity of materials can be purchased at a low price with favourable purchasing terms
- Better control on purchasing is possible
- It helps to maintain uniformity in purchasing policies
- It avoids duplication of efforts and is helpful in achieving product standards
- Transportation costs can be reduced because the bulk quantity of materials purchased
Dis Advantages of purchasing:
- Delay in receiving materials from the centralized stores by other departments
- Defective materials cannot be replaced timely
- A high initial investment has to be made in purchasing
- In the case of centralized purchasing, branches at different places cannot take advantage of localized purchasing
- There are chances of misunderstanding between the branch which requires the materials and purchasing departments with the results that wrong purchases of materials can be made.
De-centralized purchasing: decentralized purchasing refers to purchasing materials by all departments and branches independently to fulfil their needs such purchasing occurs when departments and branches purchase separately and individually. Under decentralized purchasing, there is no one purchase manager who has the right to purchase materials for all departments and divisions. The defects of centralized purchasing can be overcome by a decentralized purchasing system. Decentralized purchasing helps to purchase the materials immediately in case of an immediate situation.
Advantages of decentralized purchasing:
- materials can be purchased by each department locally as and when required
- purchase orders can be placed quickly
- no heavy investments are required initially
- transportation costs can be reduced
- rejections, shortage/ excess receipts can be settled up quickly
- materials are purchased in the right quantity of the right quality for each department easily
Dis Advantages of decentralized purchasing:
- Organizations lose the benefit of bulk purchases
- lack of proper co-operation and co-ordination among various departments
- there is a chance of over and under-purchasing of materials
- control is difficult
steps in the purchase procedure:
- Receiving purchase requisition( when to purchase?)
- Determining the purchasing quantity( how much to purchase)
- Exploring the sources of supply and choosing the supplier(where to purchase)
- Placing the purchase order and follow up
- Receiving and inspecting materials
- checking inwards invoices and passing them for payment
3Q) STORAGE OF MATERIALS:
After taking delivery of materials, it is the duty of the storekeeper to take charge. He Is the person mainly responsible for placing the material in their appropriate places inside the stores & for ensuring that they are maintained in good condition store during storage till required for utilisation in production.
Why Efficient storing?
- To hold in proper custody all stores issue purposes
- To see that there is no theft, pilferage etc.
- To maintain a Smooth & regular flow of stores to the production Processes
Types of stores:
Centralised stores: A centralised store is the only one in the company which receives materials for and issues to all who need them. The materials required for all the departments & branches are stored and issued by only one store.
Advantages
1. Better control can be exercised over stores because all stores are located in one department.
2. investment in stock is minimum
3. Better records for comparison of price & sources of supply.
4. wastage of material can be minimised.
Disadvantages :
1. This system of stores increases transportation costs because one central store may not be near every department of the factory.
2. Delay and inconvenience may be caused to departments in issuing stores.
3. Greater risk of loss in case of fire.
4. Breakdown in transport may stop production in the department.
5. Not suitable for large companies.
Decentralised stores:
Under this type of store, independent stores are situated in various departments. purchasing and handling of material. Under this type of store, independent stores are situated in various departments. purchasing and handling of materials are undertaken by each and every department separately. The departments requiring stores can draw from their respective stores situated in their departments. The disadvantages of centralised stores can be eliminated if there are decentralized stores.
Advantages
- delay in material handling will be eliminated
- minimises the chances of loss by fire
- specific needs of individual departments can be easily fulfilled
- no need of internal transportation costs
Dis advantages
- higher cost of supervision
- more space is required for individual departments
- higher amount of investment is required
- higher cost of staff and stationery
store keeper duties: All manufacturing concerns appoint a person known as storekeeper , the stores supervisor who is in charge of the store department and is responsible for store control. the storekeeper should have the technical knowledge and ability of organising the operations of the stores. The following are the duties and responsibilities of store keeper.
- receiving the stores correctly
- entering all receipts regularly in the bin cards( quantitative records of store receipts, issue, balance)
- maintaining the stores in an orderly manner so as to facilitate easy handling and physical verification of stores and prevention of loss in storage.
- ensuring that the stocks don't exceed the minimum level nor go below the minimum level
- report on waste and scrap material, obsolete stock
- prevent unauthorised persons from entering the stores
- protect/preserve stores
- maintain proper records of receipt, issue and balances
- carrying out a regular review of the items of stores for locating slow-moving and non-moving items
Requisitioning for stores: one of the functions of a storekeeper is to requisition stores for replenishment( restoration of a stock). the purchasing department places orders for materials on the basis of such requisition. Therefore, the quantity to be maintained in the requisition should be determined. In this order the guiding factors for storekeepers will be:
1. maximum stock level
2. minimum stock level
3. re-order level
4. economic order quantity( EOQ)
5. Average stock level
1. Maximum stock level: It is the highest level of quantity for any material
which can be held in stock at any time. Any quantity beyond this level causes an extra
amount of expenditure due to engagement of funds, cost of storage, obsolescence etc
It can be calculated as below:
Maximum Stock Level = Re-order Level + Re-order Quantity - (Minimum
Consumption Rate × Minimum Re-order Period)
2. Minimum Stock Level: It is the lowest level of material stock, which must be
maintained in hand at all times so that there is no stoppage of production due to the non-availability of inventory.
It is calculated as below:
Minimum Stock Level = Re-order Stock Level - (normal Consumption Rate × normal Re-order Period)
3. Re-order Stock Level (ROL): This level lies between the minimum and maximum levels in such a way that before the material ordered is received into the
stores, there is sufficient quantity in hand to cover both normal and abnormal
consumption situations. In other words, it is the level at which fresh orders should be placed for replenishment of stock.
It is calculated as:
ROL = Maximum consumption X maximum re order period
4. Re-Order Quantity: Re-order quantity is the number of materials for which
purchase requisition is made by the store department. While setting the quantity to be
re-ordered, consideration is given to the maintenance of the minimum level of stock, reorder level, minimum delivery time and most important the cost. Hence, the
quantity should be where the total carrying cost and ordering cost are at a minimum. For this purpose, an economic order quantity should be calculated.
Economic Order Quantity (EOQ): The size of an order for which the total ordering
and carrying costs are minimum.
Ordering Cost: Ordering costs are the costs which are associated with the purchase
or order of materials such as the cost to invite quotations, documentation works like
preparation of purchase orders, employee cost directly attributable to the
procurement of material, transportation and inspection cost etc.
Carrying Cost: Carrying costs are the costs for holding/ carrying inventories in
store such as the cost of funds invested in inventories, cost of storage, insurance
cost, obsolescence etc.
The Economic Order Quantity (EOQ) is calculated as below:
Annual Requirement (A)- It represents the demand for raw material or Input for a year.
Cost per Order (O) - It represents the cost of placing an order for purchase.
Carrying Cost (C) – It represents the cost of carrying average inventory on annual basis.
Assumptions underlying E.O.Q.: The calculation of the economic order of material to
be purchased is subject to the following assumptions:
(i) Ordering cost per order and carrying cost per unit per annum are known and
they are fixed.
(ii) Anticipated usage of material in units is known.
(iii) Cost per unit of the material is constant and is known as well.
(iv) The quantity of material ordered is received immediately i.e. the lead time is zero
5. Average Stock Level: This is the quantity of material that is normally
held in stock over a period. It is also known as the normal stock level.
It can be calculated as below:
Average Stock Level = Maximum Stock Level + Minimum Stock Level / 2
6. Danger level: It is the level at which normal issues of the raw material
inventory are stopped and emergency issues are only made.
It can be calculated as below:
Danger Level = Average Consumption* × Lead time for emergency purchase
*Sometimes minimum consumption is also used.
7. Buffer Stock: Some quantity of stock may be kept for a contingency to be
used in case of sudden order, such stock is known as buffer stock.
When the materials are purchased the level keeps rising. It may reach the maximum
level if the rate of issuance is less. As the materials are consumed, the stock level
starts declining. At the re-order level, reorder quantity is ordered and fresh supplies are
normally received when stocks reach the minimum level. The time interval between reorder level, when the fresh order is placed, and the time of actual receipt of
materials is known as lead time.
4Q) Methods of pricing of issue of materials:
Materials issued from stores should be priced at the value at which they are carried
in stock. But there can be a situation where the material may have been purchased
at different times and at different prices with varying discounts, taxes etc. Because
of this, the problem arises as to how the material issues to production are to be
valued. There are several methods for tackling this situation. The cost accountant
should select the proper method based on the following factors:
1. The frequency of purchases, price fluctuations and their range.
2. The frequency of issue of materials, relative quantity etc.
3. Nature of cost accounting system.
4. The nature of business and the type of production process.
5. Management policy relating to the valuation of closing stock.
Several methods of pricing material issues have evolved in an attempt to
satisfactorily answer the problem. These methods may be grouped and explained as follows:
1 Cost Price Methods
(i) Specific Price Method: This method is useful, especially when materials are
purchased for a specific job or work order, as such materials are issued
subsequently to that specific job or work order at the price at which they were
purchased.
To use this method, it is necessary to store each lot of material separately and
maintain its separate account.
Advantages
• The cost of materials issued for
production purposes to specific jobs
represents actual and correct costs.
• This method is difficult to operate,
especially when purchases and
issues are numerous.
Disadvantage:
• This method is best suited for nonstandard and specific products.
(ii) First-in First-out (FIFO) method: It is a method of pricing the issues of
materials, in the order in which they are purchased. In other words, the materials
are issued in the order in which they arrive in the store or the items longest in stock
are issued first. Thus each issue of material only recovers the purchase price which
does not reflect the current market price.
This method is considered suitable in times of falling prices because the material
cost charged to production will be high while the replacement cost of materials will
be low. But, in the case of rising prices, if this method is adopted, the charge of
production will be low as compared to the replacement cost of materials.
Consequently, it would be difficult to purchase the same volume of material (as in
the current period) in future without having additional capital resources.
Advantages
• It is simple to understand and easy
to operate.
• Material cost charged to production
represents the actual cost with which
the cost of production should have
been charged.
• In the case of falling prices, the use
of this method gives better results.
• Closing stock of material will be
represented very closely at the current
market price
Disadvantages
• If the prices fluctuate frequently, this method may lead to a clerical error.
• Since each issue of material to production is related to a specific purchase price, the costs charged to the same job are likely to show a variation from period to period.
• In the case of rising prices, the real profits of the concern are low, while the profits in the books will appear high. This may lead to the inability of the firm to meet the materials purchase demand at the current market price
(iii) Last-in-First-out (LIFO) method:
It is a method of pricing the issues of
materials on the basis of the assumption that the items of the last batch (lot)
purchased are the first to be issued. Therefore, under this method, the prices of
the last batch (lot) is used for pricing the issues, until it is exhausted, and so on.
If however, the quantity of the issue is more than the quantity of the latest lot, then the earlier (lot) and its price will also be taken into consideration.
During an inflationary period or period of rising prices, the use of LIFO would
help to ensure that the cost of production determined on the above basis is
approximately the current one. This method is also useful especially when there is a
feeling that due to the use of FIFO or average methods, the profits shown and tax
paid are too high.
Advantages
• The cost of materials issued will be
either nearer to and or will reflect
the current market price. Thus, the
cost of goods produced will be
related to the trend of the market
price of materials. Such a trend in the price of materials enables the
matching of the cost of production with
current sales revenues.
• The use of the method during the
period of rising prices does not reflect
undue high profit in the income
statement as it was under the first-in-first-out or average method. In fact, the
profit shown here is relatively lower
because the cost of production takes
into account the rising trend in material prices.
• In the case of falling prices profit
tends to rise due to lower material
costs, yet the finished products
appear to be more competitive and
are at market price.
• Over a period, the use of LIFO helps
to iron out the fluctuations in profits
• In the period of inflation LIFO will tend
to show the correct profit and thus
avoid paying undue taxes to some
extent.
Disadvantages:
• Calculation under the LIFO system becomes complicated and cumbersome when frequent purchases are made at highly fluctuating rates.
• Costs of different similar batches of
production carried on at the same
time may differ a great deal.
• In times of falling prices, there will
be a need for writing off stock value
considerably to stick to the
principle of stock valuation, i.e., the
cost or the market price whichever is lower.
• This method of valuation of
material is not acceptable to the
income tax authorities.
2. Average Price Methods
(i) Simple Average Price Method: Under this method, materials issued are
valued at the average price, which is calculated by dividing the total rates at which a different lot of materials are purchased by the total number of lots. In this method
quantity purchased in each lot is ignored. However, the price of the stock of that lot
which is completely sold out is not considered for taking the average price.
This method is suitable when the materials are received in uniform lots of similar
quantity, and prices do not fluctuate considerably.
Advantages
• This method is simple to use for an
entity which orders materials in a
lot of standard quantity, as only
price per lot is taken to calculate the average price
.
• In a stable price environment, this
method gives a price which
approximates to the current
market price.
Disadvantages
• This method does not provide the right stock valuation when the standard quantity for purchase in a lot is not specified
• When the price of materials fluctuates and the entity chooses to customise the order quantity, the price under this method may differ substantially from the current market price.
(ii) Weighted Average Price Method:
Unlike the Simple Average Price method,
this method gives due weightage to quantities also. Under this method, the issue price
is calculated by dividing the sum of products of price and quantity by the total number of quantities.
Advantages
• It smoothens the price
fluctuations, if at all it is there,
due to material purchases.
• Issue prices need not be
calculated for each issue unless a new lot of materials is received.
Disadvantages
• Material cost does not represent the actual cost price and therefore, a different profit or loss will arise out of such a pricing method.
• It may be difficult to compute since every time a lot is received, it would require a re-computation of issue prices.
3 Market Price Methods
(i) Replacement Price Method: Replacement price is defined as the price at
which it is possible to purchase an item, identical to that which is being replaced
or revalued. Under this method, materials issued are valued at the replacement cost
of the items. This method pre-supposes the determination of the replacement cost of
materials at the time of each issue; viz., the cost at which identical materials could be
currently purchased. The product cost under this method is at the current market price,
which is the main objective of the replacement price method.
This method is useful to determine the true cost of production and to value material
issues in periods of rising prices because the cost of material considered in the cost of
production would be able to replace the materials at the increased price.
(ii) Realisable Price Method: Realisable price means a price at which the
material to be issued can be sold in the market. This price may be more or may
be less than the cost price at which it was originally purchased. Like the replacement
price method, the store's ledger would show profit or loss in this method too.
Comments
Post a Comment